- Home
- Order Entry and Customers
- Back Ordering
Back Ordering
This FAQ will go over Back Orders in Paradigm. A back order is when a certain product is out of stock, but is expected to be delivered once the product is back in stock.
Paradigm will prompt the user to create a back order during invoice posting when the pieces shipped on the invoice is less than the pieces ordered.
Note that often times it is cleaner to split the order before invoicing instead of creating a back order. More information on splitting orders can be found here: Splitting Orders
Back orders quantities can be recorded in Fulfillment Pro as well: Fulfillment Pro: Back Ordering
Standard Back Ordering Process
Change the pieces shipped on the invoice to less than pieces ordered, then post the invoice and Paradigm will ask to create a back order.

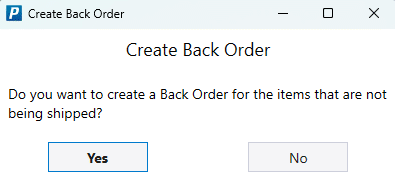
Select the lines to include on the back order and click “Create Back Order”
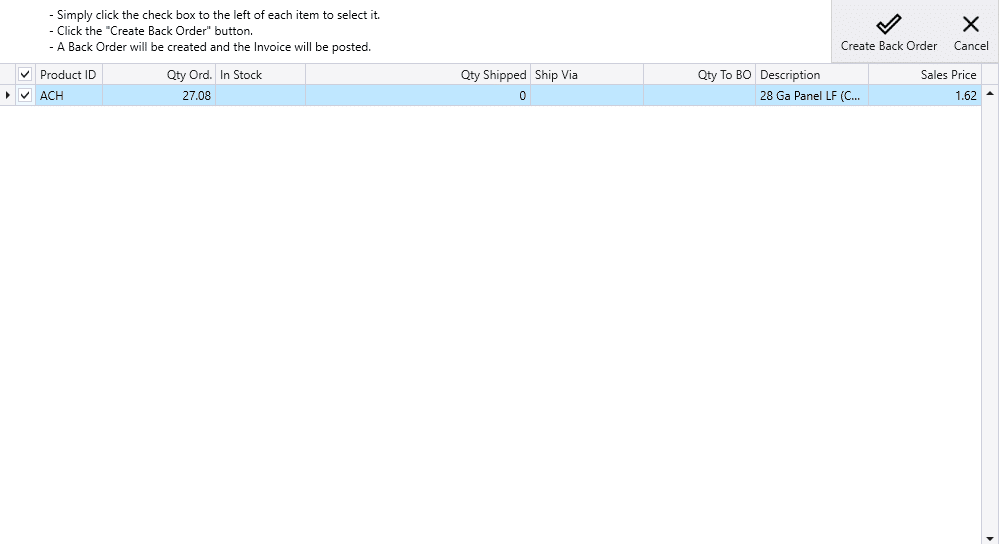
The created back order is just for the unshipped products. Creating a back order for an order line that has pull labels will re-assign un-shipped pull labels to the back order if possible. If the label cannot be automatically moved, it will leave it unchanged and add “[This line may have been pulled on the original order]” to the line description.
This will be shown as a new order but the production information is retained from the original order so items won’t get produced twice. The back order can then be processed like any other released order to get it shipped again when the product is back in stock.
It is recommended to set the ship date on the back order to the estimated restock date of the product.

Recording Back Orders Before Invoice
To select a quantity to back order before invoicing, go to the order detail line’s line item options popup.

Enter the pieces to back order in the “Qty to backorder” field. This will automatically be deducted from the pcs shipped when converting the order into an invoice.
Back orders recorded in Fulfillment Pro will be reflected in this field as well.
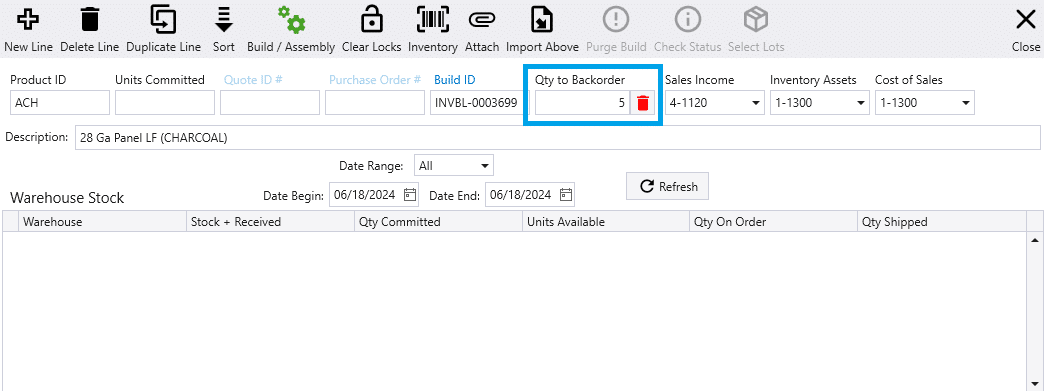
Contents
Categories
- Purchase Order and Vendors (19)
- Production (34)
- Order Entry and Customers (75)
- NEW! (6)
- Job Costing (16)
- Inventory and Pricing (92)
- General (54)
- Fulfillment Pro (29)
- Dispatching (23)
- Administration and Setup (39)
- Add-Ons and Integrations (29)
- Accounting (51)