- Home
- Inventory and Pricing
- How To Manage Manufactured Item Pricing
How To Manage Manufactured Item Pricing
This FAQ will go over the recommended process for calculating and updating manufactured to order item pricing. This is done by using cost-based pricing with markups for all manufactured items or each profile. When coil costs change, the updated cost will adjust the sales prices of the manufactured items after it has been cascaded using the “Edit Pricing” tool.
Calculate Pricing
To calculate pricing, use a pricing method based on cost and choose a mark up percent. The sales price will automatically be updated whenever the cost is updated.
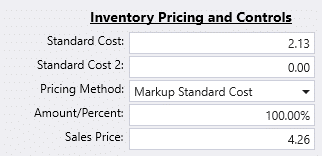
Updating Cost
To update the cost for manufactured items, the “Edit Pricing” tool can be used. Filter the list down to the items that are going to be updated. Select the “Cost” column and then “Assembly Cost” from the drop down. This will update the cost to the total assembly cost for the item.
This should be done after coil costs are updated, to cascade the updated cost down to the manufactured products.

The reason cost is updated based on the “Standard Cost” instead of the “Current Cost”, is to prevent mistakes or very minor changes in cost from affecting pricing. For example if one color was bought in higher than the other colors, using current cost would cause that color to be more expensive. Or if a cost was entered incorrectly, items would be priced much too high or low without notice.
Contents
Categories
- Purchase Order and Vendors (19)
- Production (34)
- Order Entry and Customers (75)
- NEW! (6)
- Job Costing (16)
- Inventory and Pricing (92)
- General (54)
- Fulfillment Pro (29)
- Dispatching (23)
- Administration and Setup (39)
- Add-Ons and Integrations (29)
- Accounting (51)